A plumbing system delivers water to fixtures and appliances and carries wastewater and sewage away from a dwelling. The pipes in a plumbing system are usually made of cast iron, copper or plastic.
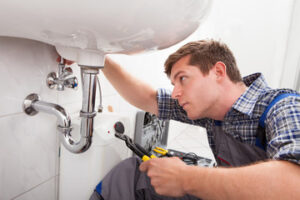
A rough-in plumbing diagram is a linear drawing that uses lines and symbols to display the layout of the venting and drainage pipes behind walls and under floorboards. It is required for most construction projects and often submitted with blueprints for permit applications. Visit https://www.plumbing-express.com/ to learn more.
A well pump is the heart of a water system. It is critical that this pump be in good condition and capable of performing its intended function. The pump must be able to sustain the full pressure of your well and piping systems. It must be able to prevent backflow, upthrust and water hammer. This can be achieved by regularly checking the pump’s condition and having it tested for proper operation.
The check valve is an essential device to help prevent backflow and prevent water hammer. A check valve is a one-way valve that stops fluid flow in the opposite direction of normal flow. There are many different types of check valves, but the most common ones use a ball bearing retained by a spring. When the pump stops, the pressure will reverse and force the ball bearing to compress against the opening, stopping flow.
This rapid dissipation of energy prevents the shock of backflow that can cause a surge that damages piping and equipment in your well system. The check valve also prevents upthrust from occurring by forming a tight seal against the pipe wall.
Clean the Pump
If your sump pump is contaminated with mold or grime, it will not work properly and could damage the float switch or other components. Clean the pump by starting with the interior, using a solution of vinegar and water to dissolve mineral deposits and grease. Scrub the inside thoroughly and rinse. Before moving to the exterior, wipe down the surfaces with disinfectant wipes, especially if you are sharing a pump with others.
Next, locate and remove the inlet screen. This is typically a filter-like component that prevents debris from entering the pump. Clean it thoroughly with soapy water, and be sure to scrub the float switch to ensure that it can move freely without causing damage or hindering performance.
After scrubbing the pump and its components, splash water on the pump with the garden hose to flush down and loosen any remaining debris and gunk. You may also want to use a plastic scraper or other tool to loosen any hard-to-remove residues and dirt.
Finally, sanitize the pump kit, bottle brushes and wash basins. There are several methods for sanitizing these items, so check the manufacturer’s instructions and follow them closely. You may need to steam disassembled pump parts and wash basins or boil them. Be sure to allow the items to air-dry completely before storing them. This will help prevent germs and mold from growing on them during storage.
Check the Check Valve
A check valve prevents backflow by allowing fluid or gas to flow in one direction and blocking it from flowing backward. Its operation is simple. The disc or ball in the valve pushes off the seat to open and let fluids or gases flow through the check valve. If the pressure behind the valve falls below a threshold known as the cracking pressure or if there is backflow, the disc closes to stop what has already passed through the valve from entering in the opposite direction.
Check valves come in a wide range of sizes and types. They may have socket weld, threaded, flanged or wafer end connections. They are made from a wide variety of materials, including bronze, cast iron, stainless steel and various alloys such as Hastelloy and Inconel. They are designed for use in a variety of applications and operating conditions, such as submerged, above-ground, horizontal or vertical installations.
The type of material a check valve is made from is important because it must be compatible with the liquid or gas that will flow through it. The body of the valve and the seat it seals against must be non-corrosive. Sanitary check valves are manufactured to allow for clean-in-place procedures, which means they must be easy to disassemble and sterilize. They are typically made from materials that can withstand harsh chemicals and high temperatures.
If you choose the wrong check valve for your application, it can wear out quickly. The best way to reduce the chance of this is to choose a valve that matches your application and working conditions. You also need to regularly inspect the valve and its components.
Flow rate is another factor to consider. If the check valve is used in a system with a very fast flow rate, it can wear out prematurely. This is especially true of metal-seated check valves. Flow turbulence causes vibration that damages pipes and fittings and can even destroy the valve itself.
The location of the check valve is also important, as it should be away from a pump or other device that could be damaged by a sudden drop in fluid pressure. Ideally, there should be at least 10 pipe diameters of straight, unobstructed pipe upstream and downstream of the valve. This allows for a smooth and laminar flow, which is best for check valve operation.
Test the Pump
When it comes to water-based fire protection systems, the pump is the heart of the operation. Its condition determines how much pressure is available to supply the system during an emergency. To ensure that it works as intended, the pump must be tested regularly. When doing so, it is important to evaluate both the net and gross performance of the pump. Net performance measures the amount of work the pump is doing versus the load it is carrying, while gross performance measures the system discharge pressure.
During the test, the pressure is gradually increased from the system reservoir until the pump reaches its rated performance. The test should also be conducted at the lowest point of access for the system, to minimize the risk of ruptured pipes. If the system has pressure relief valves, they should be temporarily disabled during the test, to prevent dangerous releases.
The test is typically performed by a certified testing company. The firm will first verify that the system has all required connections and is free of debris and damage. Then, it will pressurize the system with water (or other liquid), and monitor it for pressure drops. If significant drops occur, they can indicate a leak or other problem. A dye may be used to help distinguish test fluids from system water.
While the system is under pressure, inspectors check the integrity of the piping and joints. They can spot problems that might not show up during a visual inspection, such as leaking or missing connections. It is important to identify these issues proactively, because they could prevent the system from delivering sufficient water during an emergency.
A hydrostatic test pump RP50 is an essential tool for all fitters. It enables them to perform quick and precise compression tests and leak tests on piping systems and containers, such as those found in plumbing and heating installations, sprinkler and boiler installation, and pressure vessel manufacture. With a simple design, it is easy to use and provides accurate readings in bar, psi or MPa. It has a rugged handle hinge and long piston for low-wear, precision pressure transmission, plus a built-in shut-off valve and weather proof cover.