3D Printing Arizona turns digital models into physical objects. It is used for prototyping, reducing manufacturing costs, and enabling on-demand production.
It is also transforming supply chains, making businesses less dependent on suppliers that can be affected by geopolitical tensions that delay shipping. It puts manufacturing in the hands of companies themselves.
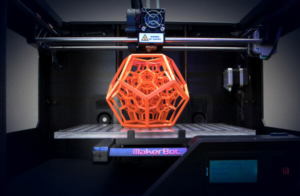
3D printing is a great way to prototype new designs and test them out. It also offers the advantage of a quick turnaround, which is important when collaborating with clients. However, it is important to note that the quality of 3D prints can vary widely. This can be a result of a number of factors, such as the type of printer used and the quality of the material. The process of creating a 3D print requires a lot of precision, so it is crucial to choose the right materials and design the object properly.
In addition to prototyping, 3D printing can be used for many other applications. For example, it can be used to create jigs and fixtures for manufacturing operations. This helps reduce the cost of manufacturing and improves accuracy. It can also be used to create parts for repairs or replacements, which saves time and money. 3D printing can be used to make complex geometries that are difficult to manufacture using traditional methods.
Another benefit of 3D printing is the ability to use multiple material types. This allows designers to use more complex shapes and reduce the weight of the final product. Additionally, it can save a significant amount of energy compared to other manufacturing technologies. In addition, it can be used to produce a wide range of colors and finishes. In the past, this technology was mainly used for prototyping, but it has now expanded to include the production of functional parts.
Moreover, it can be used to replace injection molds and jigs. This can help businesses save money and time by avoiding the expense of purchasing and maintaining these tools. This also eliminates the need for a separate assembly line for making injection molds and jigs.
Finally, it can be used to produce components for medical and aerospace applications. These components can be printed from titanium, cobalt, or aluminum, and they are more durable than traditional metal parts. They are also lighter and stronger. For instance, GE Aviation’s LEAP engine uses 3D-printed Cobalt-chrome fuel nozzles that weigh 25 percent less and are five times as strong as the conventional version.
Applications
3D printing is a valuable tool for companies across many industries. It can produce items with geometries that are difficult, or even impossible, to create using traditional manufacturing methods. In addition, it can reduce manufacturing costs by enabling manufacturers to keep production in-house rather than outsourcing. 3D printing is also useful for creating prototypes for industrial goods, allowing companies to reduce their lead times and stay competitive.
The technology can be used to make complex models and scale models of buildings, cars, and other large structures. This can help engineers test their designs and improve the quality of final products. In addition, it can be used to create replacement parts for existing equipment. 3D printing is particularly useful for making custom parts, as it can save time and money compared to sourcing the components from external suppliers.
In the aerospace industry, 3D printing is helping to develop innovative new designs and parts that would be difficult or expensive to manufacture using conventional methods. For example, one company has created a 3D-printed jet engine component that is lighter and more efficient than its traditional counterpart. This reduction in weight has the potential to increase fuel efficiency and reduce emissions.
Industrial goods manufacturers are also embracing the technology for its ability to provide rapid prototyping. This enables them to bring new products to market faster by bypassing the time-consuming and costly tooling production step. It is also allowing them to respond to customer demand by producing parts on-demand. According to the Sculpteo State of Industry report, 52% of those within the industrial goods sector say that they use 3D printing for this reason.
3D printing is also useful for manufacturing spare parts for industrial machinery, such as printers and electronics. It can be used to produce parts with complex geometries that are difficult or impossible to produce using traditional methods, and it can be used to replace obsolete parts. In addition, it can be used to make spare parts for older machines by reducing maintenance costs and avoiding the need to buy replacements.
Another use of 3D printing is in medical technology. For example, a mountaineer was able to walk and climb again after having a hip replacement made with a 3D-printed acetabular cup. The part mimicked the porous structure of natural bone, which helped in osseointegration and improved his recovery.
Costs
There are a number of costs associated with 3D printing, including material, energy, and maintenance. To determine how much a project will cost, you need to consider all of these factors, and then compare them to the final cost of the product. This way, you can make the most informed decisions and optimize your processes for quality and cost-effectiveness.
3D printing is an excellent choice for prototyping products because it allows engineers and designers to make changes to their designs quickly and efficiently. In addition, 3D printing reduces the time it takes to get a finished part from design to production, which means that companies can respond to customer demands and improve their bottom line.
However, while the benefits of 3D printing are obvious, many people wonder how much it costs to actually print something. The answer to this question depends on a variety of factors, such as the type of printer, materials, and complexity. In addition, the length of the print and the amount of time it takes to print can also impact the final cost.
One of the biggest costs associated with 3D printing is the material itself. Most standard printer filaments cost around $20 per kilogram, while more specialized materials can cost as much as $120. These costs can add up quickly, especially if you are printing large models.
Another significant cost associated with 3D printing is the electricity used to run the printer. On average, an entry-level printer consumes 50 to 70 watts of power per hour. This isn’t a lot of energy, but if you are running a business that prints several models daily, this can add up over the long term.
Finally, there are the labor costs associated with 3D printing. This includes the time it takes to prepare and operate the printer, as well as the time that it takes to finish and sand the printed parts. It is also important to remember that the printer will need regular maintenance, such as replacing nozzles and cleaning the build plate.
There are a number of free and paid 3D printing calculators available on the internet that will help you calculate how much your prints will cost. These calculators will usually account for the major cost factors mentioned above. However, it’s important to remember that these tools are only approximate estimates and should be viewed as a starting point for your project.
Technology
3D printing is a process of creating physical objects by layering different materials to form the desired shape. The result is complex structures that can vary in size, rigidity, and color. The technology is being used to build prototypes, parts for manufacturing and a range of other applications. It is also being considered as a method for constructing entire buildings.
The origins of 3D printing date back to the 1980s when Japanese inventor Hideo Kodama patented the first rapid prototyping machine. Chuck Hull later patented stereolithography, enabling commercial 3D printers to be sold. He also created the STL file format and founded 3D Systems Corporation.
In addition to lowering costs, 3D printing can speed up the design and development of new products. Unlike traditional manufacturing, which requires machining or milling to create a part, 3D printing allows for the creation of complex geometries in a fraction of the time. This can reduce the number of components needed for a product, which can significantly lower its total cost. The technology also allows for the use of lighter and more durable materials than conventional alternatives, reducing its weight and energy consumption.
While plastics and metals are the most common materials used for 3D printing, a wide variety of other materials can be used. This opens the door for the development of custom-tailored materials with particular properties, such as water resistance or higher strength for specific applications.
In medical applications, physicians are using 3D printing to make surgical guides and orthopedic implants. They are also using it to create patient-specific replicas of bones and organs for surgery. The process is also being used to print prosthetics and artificial teeth, as well as to recreate human tissues from CT scans.
The process produces waste in the form of uncured filament and powders, which must be disposed of properly. It may also produce harmful vapors and particulate matter when melting or sintering plastic filaments in processes such as fused deposition modeling (FDM) and selective laser sintering (SLS), or when sintering metal powder in DMLS and electron beam melting (3D printing). To mitigate these risks, proper ventilation and protective equipment must be utilized.